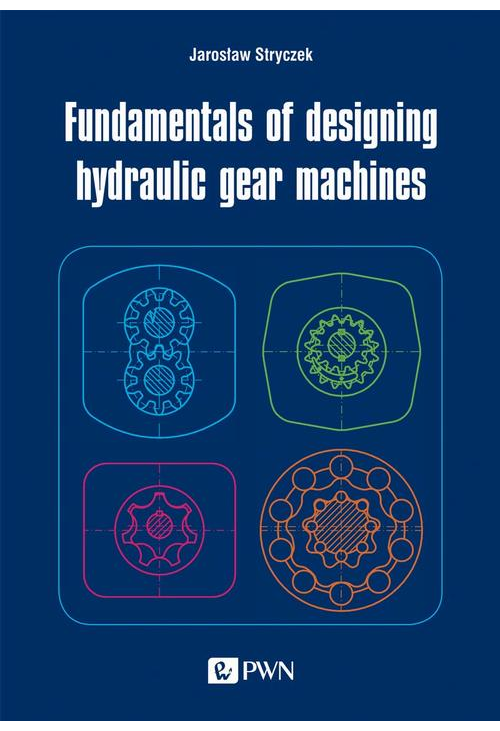
- -11%
ebook Fundamentals of designing hydraulic gear machines
Fundamentals of designing hydraulic gear machines to kompleksowe wprowadzenie do projektowania maszyn przekładniowych z napędem i sterowaniem hydraulicznym. Autor, Jarosław Stryczek, dzieli się swoją wiedzą zdobytą podczas ponad czterdziestoletniego doświadczenia w tej dziedzinie.
Wydane przez Wydawnictwo Naukowe PWN w 2020 roku, ta publikacja jest napisana po angielsku i skierowana zarówno do inżynierów, jak i studentów mechaniki oraz technologii płynowej.
Maszyny przekładniowe hydrauliczne (HGM) odgrywają kluczową rolę w systemach napędowych i sterujących, gdzie przekładnie są głównym elementem zarówno pod względem projektu, jak i zasady działania. HGM-y znajdują zastosowanie w przekształcaniu energii mechanicznej na hydrauliczną lub odwrotnie - jako pompy lub silniki hydrauliczne.
Jarosław Stryczek, będący członkiem Grupy Badawczej Napędu Hydraulicznego przy Wydziale Mechanicznym Politechniki Wrocławskiej, podzielił się swoimi doświadczeniami i wiedzą w tej dziedzinie.
Jeśli interesują Cię ebooki naukowe, literatura techniczna lub poszukujesz bestsellerów z dziedziny mechaniki płynowej, ten tytuł jest dla Ciebie! Dostępny w wydaniu elektronicznym w formacie PDF, łatwo pobierzesz go ze sklepu z ebookami.
Zanurz się w świat hydrauliki i naucz się projektować wydajne maszyny przekładniowe za pomocą tego praktycznego i przystępnego podręcznika.
Szczegóły ebooka Fundamentals of designing hydraulic gear machines
- Wydawca:
- Wydawnictwo Naukowe PWN
- Rok wydania:
- 2020
- Typ publikacji:
- Ebook
- Język:
- angielski
Recenzje ebooka Fundamentals of designing hydraulic gear machines
-
Reviews (0)

Na jakich urządzeniach mogę czytać ebooki?
- -11%

@CUSTOMER_NAME@
@COMMENT_TITLE@
@COMMENT_COMMENT@